Picking Best Practices with SAP Extended Warehouse Management (SAP EWM)
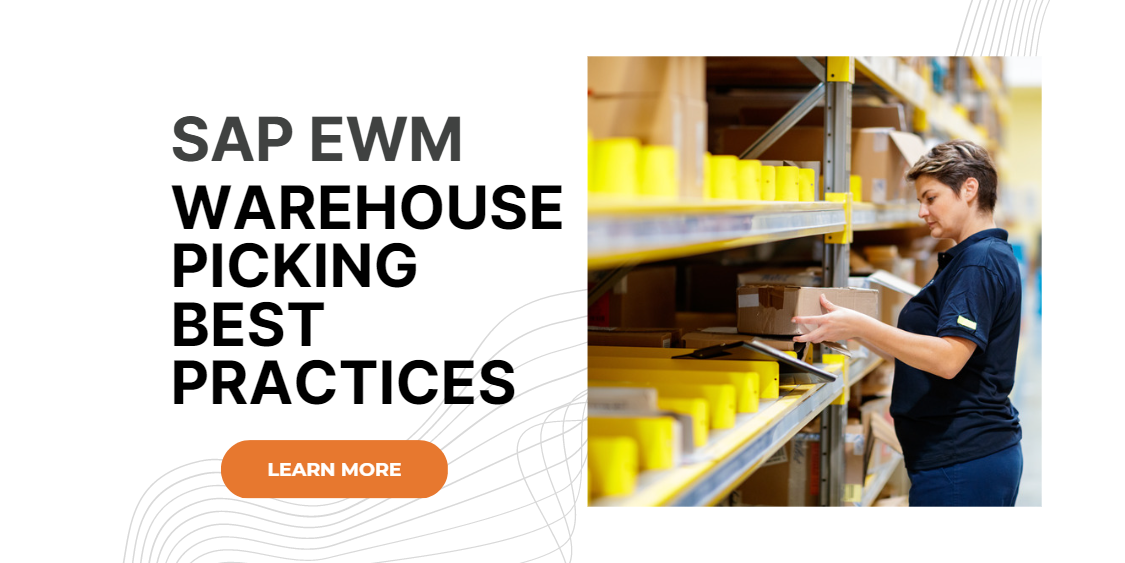
The picking process implemented in your SAP-run warehouse will significantly impact supply chain performance. Surprisingly, many supply chain intensive organisations fail to recognise critical inefficiencies when running SAP Extended Warehouse Management (SAP EWM), and it’s time to address this.
For warehouses that rely on SAP Extended Warehouse Management (EWM) tools, the ability to integrate and apply people-centric mobile experiences that ensure picking is quick, accurate, safe and timely is essential for long-term operational success. The key performance indicators for this success will help you maximise efficiency gains in your warehouse picking strategy.
In this article, we look at five key areas that affect picking quality and output in your SAP-run warehouse; we then delve deeper into the SAP EWM and Mobile best practices that apply to warehouse picking processes and suggest ways to action practical improvement strategies.
1. Layout
A well-laid-out warehouse that implements clear signage and labelling best practices is foundational for any process, warehouse management software, or technology improvement that you may be looking to introduce.
1a. Clear signage and labelling
It may sound obvious, however, a surprisingly large number of warehouses lack clear signage in the aisles, storage areas, and bins; these are often neglected or not in line with the processes and technology being used. It’s frequently the case that warehouse operations grow reliant on people’s ability to remember where things are located throughout the warehouse; this is neither sustainable nor effective in the long run.
It’s time to take a human and technology-friendly approach to warehouse signage. Start by applying logic, consistency, and clarity to signage and labelling. Think about the material handling equipment and the technology (scanning/imaging/barcode/RFID) involved in each process and the type of information required –– ideally, as part of your layout and process design. Don’t overlook the need for clear human-readable information in addition to barcodes for area/aisle/bin identification. If you are using voice technology, spoken check digits make for fast, easy verification.
Demarcate and delineate open storage or floor spaces reserved for interim stock holding. These areas are often high-congestion zones in many warehouses and vulnerable to overflow; they’re also likely to cause delays as they can easily become chaotic and mismanaged areas.
How SAP EWM can help
Correctly aligning warehouse layout master data with warehouse signage, storage, and bin types is straightforward, as is the addition of verification data for barcode or human-readable bin labels. Furthermore, physical layouts can be accurately mapped in three dimensions (3D) to drive work and travel time calculations for work planning and labour management.
Access our easy-to-follow self-assessment and highlight the performance, productivity and people benefits lying dormant in your current SAP-run warehouse picking strategies.
Score your warehouse today by downloading the free questionnaire here.
1b. Activity-based layout
The design of warehouse picking processes and layout are intrinsically linked. A layout that works for one type of picking method, may cause congestion or inefficiencies in another. Choosing the optimal storage bin types, layout, and walk sequences for the kind of activities you have is crucial. For example, an e-commerce operation might benefit from high-density picking areas with access to a wide range of products. In a business-to-business (B2B) product/carton scenario where one order is picked at a time, a walk sequence that allows for the order to be built up progressively without excessive travel time will likely be beneficial. Full palette operations, on the other hand, will want to spread the work out to avoid aisle or pick-up and drop-off (P&D) congestion.
How SAP EWM can help
A variety of warehouse picking strategies exist for specific pick-types. The most appropriate picking strategy is used, automatically based on flexible rules based on the warehouse layout (Layout Oriented Storage Controls) and Process (Process Oriented Storage Controls).
2. Pick Planning
While low-volume warehouses can often manage with a more drip-fed or sporadic release of work into the warehouse, operating effectively at higher volumes (or nearing space or resource capacity limits) will benefit significantly from pick planning. Combined, the three points discussed below will give logically-sized pick waves that are easier to manage and ensure consistent completion –– on time and in full.
2a. Layout capacity
Any workload released into a warehouse needs to take into account the constraints that the physical layout imposes on picking output. When planning picking activities, consider the physical capacity of interim storage areas, such as P&D points, packing areas, and staging lanes. Any plan should release work in a way that avoids bottlenecks or overflows in these areas.
How SAP EWM can help
As part of setting up the warehouse layout, the different storage capacity and capacity checks of the storage types and bins can be set to ensure the physical constraints are always respected, avoiding overflows or incorrect placement instructions. Various factors like product type, weights, volumes, packaging material can all be considered
2b. Using expected effort and time windows
Planning picking in a way that can be easily managed against a cut-off time makes it easier to ensure the on-time departure of goods.
Creating a pick plan that takes the resource capacity into account, along with the expected picking effort, will ensure any work is carried out within the available time, utilising the available resources. This makes the picking progress easier to monitor against the plan and keep on track.
More advanced planning can use dynamically calculated effort across picking, packing, and even value-added services, as well as travel times, to create more accurate workload estimates. Something that larger/higher volume warehouses with larger workforces can benefit from.
How SAP EWM can help
Planned despatch times are derived from customer shipping information or taken from SAP Transportation Management (SAP TM); these, combined with the expected, planned processing time of picking efforts, allow pick-wave creation to group picking together into workload fitting with the prescribed time window and with completion in time for scheduled despatch time. Furthermore, the multiple steps of the despatch process, such as packing and loading, can be included in this time window calculation.
2c. Resource planning
With seasonal peaks, a feature of many supply chains and increasing challenges in the associated availability of labour, forward planning for resource needs is essential to ensure customer demand can be picked and fulfilled on time and in full.
How SAP EWM can help
Capacity planning of resources, considering resource calendar and capacity consumption rules, allows accurate picking planning, taking into account the available resources.
Defining and understanding resource capacity is made easier by the labour management system, which is integral within SAP EWM. This captures and reports relevant operational information in real-time, allowing detailed labour management and calculation/refinement of the actual effort required to complete picking and other warehouse tasks. This allows continuous improvement and adaptation of the data, which was without a labour management system is very time-intensive to capture and maintain.
3. Mobile Execution
The benefits of mobile execution go far beyond the removal of paper from your operation. Productivity and accuracy gains, plus the benefits of real-time information throughout the supply chain, are clear. When done correctly, the workforce also benefits from better working methods, with greater flexibility and self-sufficiency driving up overall user experience improvements.
3a. Use optimised mobile picking process
Using mobile devices to carry out your picking will ensure greater speed and accuracy and, furthermore, ensure the right people carry out the right activities at the right time. However, if your mobile processes are not suitable for the type of picking, you risk slowing things down instead of speeding them up. The type of picking, the material handling equipment needed, and the type of verification data all play an important part. Pallet picking, multi-order picking, pick and pack, and where labelling is taking place will all require slightly different mobile processes to provide an optimal result.
How SAP EWM can help
Mobile execution of picking allows warehouse operators to carry out different types of picking scenarios in real-time, such as pallet picking, delivery-based carton/piece picking and pack, e-commerce (multi-order) picking, packing and loading.
3b. Ensure usability
Don’t underestimate the importance of usability. Getting it right and providing your mobile workers with an intuitive, easy-to-use mobile interface will save time, improve productivity, accuracy, and adoption. Old fashioned mobile user interfaces tend to be cluttered or badly laid out, only focusing on individual transactions and not supporting the wider user needs well, leading to lower productivity.
Think about optimising the user experience –– not just the transactions. Forward-thinking and sustainable approaches are required to ensure the person carrying out the picking has the right tools and devices to get the job done.
How SAP EWM can help
Mobile transactions can be streamlined to some extent to aid ease of use, removing data and fields not required and arranging screen layout for the specific scenario/process/device type. Two user interface styles are available, SAP ITS Mobile and SAP Fiori. These can be used as appropriate depending on the type of work being carried out.
Improvements to the user experience over the supply mobile interface can be achieved easily without disrupting standard SAP by adopting Rocket Mobile. The significantly improved user interface and a wide range of mobile capabilities make picking and other warehouse tasks faster and more intuitive. This helps to create a more self-sufficient, high-performance mobile workforce.
3c. Choose the right devices
Tailor and optimise your mobile device to the type of picking activity. For example, a traditional handheld device may be fine for a palette or box operation. In contrast, wearable or even voice-activated devices will be more suited to small-item or e-commerce picking, and vehicle-mount devices optimised for forklift or high-reach trucks will be easier to use in specific situations. Getting this right presents significant productivity gains and is more sustainable for the workforce.
Based on the type of warehouse, different devices can be chosen for picking. For example, in a manual warehouse, voice picking would be an effective picking technology, and the device used (say, a headset and voice input device) can be configured in EWM where real-time picking transactions are dictated, and they can be accessed on the go.
How SAP EWM can help
Different device form factors can be used, such as handheld, wearable, and vehicle-mounted devices, with system set-up options to tailor layouts for each. Voice and RFID picking processes can also be used where beneficial to material handling efficiency. Optimisation of transactions devices is best done by adopting Rocket Mobile, and where voice is used, specialised voice engines. Both are elegantly embedded directly within SAP, providing a seamless experience for the warehouse picker and without disrupting standard SAP software.
4. Management information
Real-time, accurate, and readily available operations management information is critical to the continued smooth running of any warehouse. It allows quick decision-making to keep picking on track and drives continuous process improvement. Correct use of operational and key performance indicators will drive accountability within the operation and increase customer service levels up.
4a. Operational reporting
Avoid using old-fashioned, siloed, list-style reporting to manage your warehouse. These can easily swamp a warehouse or process manager with data with slow analysis to derive useful information. If you see people exporting data into excel to try to understand the situation, then you are almost certainly suffering from this.
Instead, bring together the key information required to manage the operation and directly investigate and resolve issues quickly to keep picking on track.
How SAP EWM can help
The go-to console for warehouse managers using SAP EWM is the Warehouse Activity Monitor. This brings detailed operational information together in a single view, allowing quick drill down into details across processes where needed.
Complementing this with the real-time embedded smart business warehouse analytics allows process managers to instantly gain insight such as pick workload and progress.
4b. Key performance indicators
Use Key Performance Indicators (KPIs) to understand the overall performance of the warehouse, such as capacity and resource utilisation, overall productivity, and pick rates; then, tie these into operation feedback to drive the necessary improvements and changes in behaviour. Combine with Operational performance indicators (OPIs) to quickly provide an easy-to-understand view of the current situation, such as picking progress against plan. This rapid insight into what is actually happening allows quick decision-making to keep picking on time.
Consider making relevant performance indicators available to users directly as part of their mobile interface to drive accountability, quality, and productivity behaviours.
How SAP EWM can help
Real-time embedded smart business warehouse analytics allows process managers to instantly gain insight such as pick workload and progress.
4c. Live management dashboards
Use live dashboards to bring together management information showing status, OPIs and KPIs across all activities against targets and expectations. For example, pick progress against the pick plan is a great way to monitor picking activity.
How SAP EWM can help
Real-time visual warehouse KPIs are provided as standard with the SAP EWM Warehouse KPIs Fiori App, which can be easily adapted for your specific warehouse targets and measure. Deeper data analytics and visualisation can be provided with the warehouse specific analytics platform SAP Warehouse Insights
5. Emerging practices
Established best practices are at the core of any effective warehouse picking operation, but it’s also vital to look ahead if you want to be responsive to growth. Cost barriers to software and technology are lowering, with more flexible ways to deploy that reduce the associated capital expenditure. Leading organisations are already benefiting from some of these critical areas:
5a. Automation technology
For many years warehouse automation has been predominantly the ‘infrastructure’ style of Automatic Storage and Recovery Systems (ASRS), such as dense pallet storage cranes, for example. In many situations, this type of automation can provide a compelling return on investment, although typically for new-build warehouses.
However, the introduction of new small-scale autonomous robots provides a very cost-effective way of bringing automation benefits into an existing warehouse, offering more opportunities to retrofit and automate picking at a significantly lower budget.
How SAP EWM can help
An embedded material flow system (MFS) allows cost-effective integration and control of a wide range of warehouse automation, keeping all warehouse logics, master data, controls, and management centralised. Picking processes can be easily executed with a mixture of mobile workers and automation as required.
5b. Process automation
Removing manual administration steps associated with picking is a good source of cost-saving and quality improvement. Whether this be handling paper documents for audit trail, manual data input, loading of master data to despatch processes, carrier data, or other picking follow on task.
Identifying areas where paper and manual steps can be removed from the process will help streamline and ensure your picking and inventory data is up to date at all times and potentially allow you to invoice sooner. Mobile-driven activities play a crucial role, but process automation goes beyond this.
Intelligent Robotic Process Automation (RPA) and Automated Document Information Extraction are two emerging technologies that offer new tools for process automation.
How SAP EWM can help
Pairing SAP EWM with the SP Business Technology Platform opens up a wide range of RPA and document information extraction, allowing manually intensive jobs to be automated to save time and cost.
5c. Advance mobile scenarios
The evolution of mobile hardware and software has unlocked new mobile picking scenarios; photo capture can be used in traceability and quality scenarios, document and signature capture can save time and support compliance scenarios directly from the mobile device. User engagement, issue reporting, equipment inspection and many more activities can be part of your mobile worker toolkit, keeping unplanned interruptions to your picking productivity to a minimum and automating follow-on processes, such as invoicing or document attachment, for example, carrier acceptance documents.
How SAP EWM can help
Native mobile is purely focused on the provision of mobile transactions based on either barcode scanning, manual data entry or RFID data. Advanced mobile scenarios can be easily enabled with Rocket Mobile.
A proactive commitment to continuously improving warehouse processes and infrastructure will ensure a flexible and agile workforce, ensuring a profitable operation. Start by taking our free Warehouse Mobility Performance Evaluation. This easy-to-follow self-assessment will highlight the performance, productivity and people benefits lying dormant in your current processes. See how your warehouse scores by downloading the free questionnaire here.