SAP Planning Implementation: Real-time Installation Promise Dates
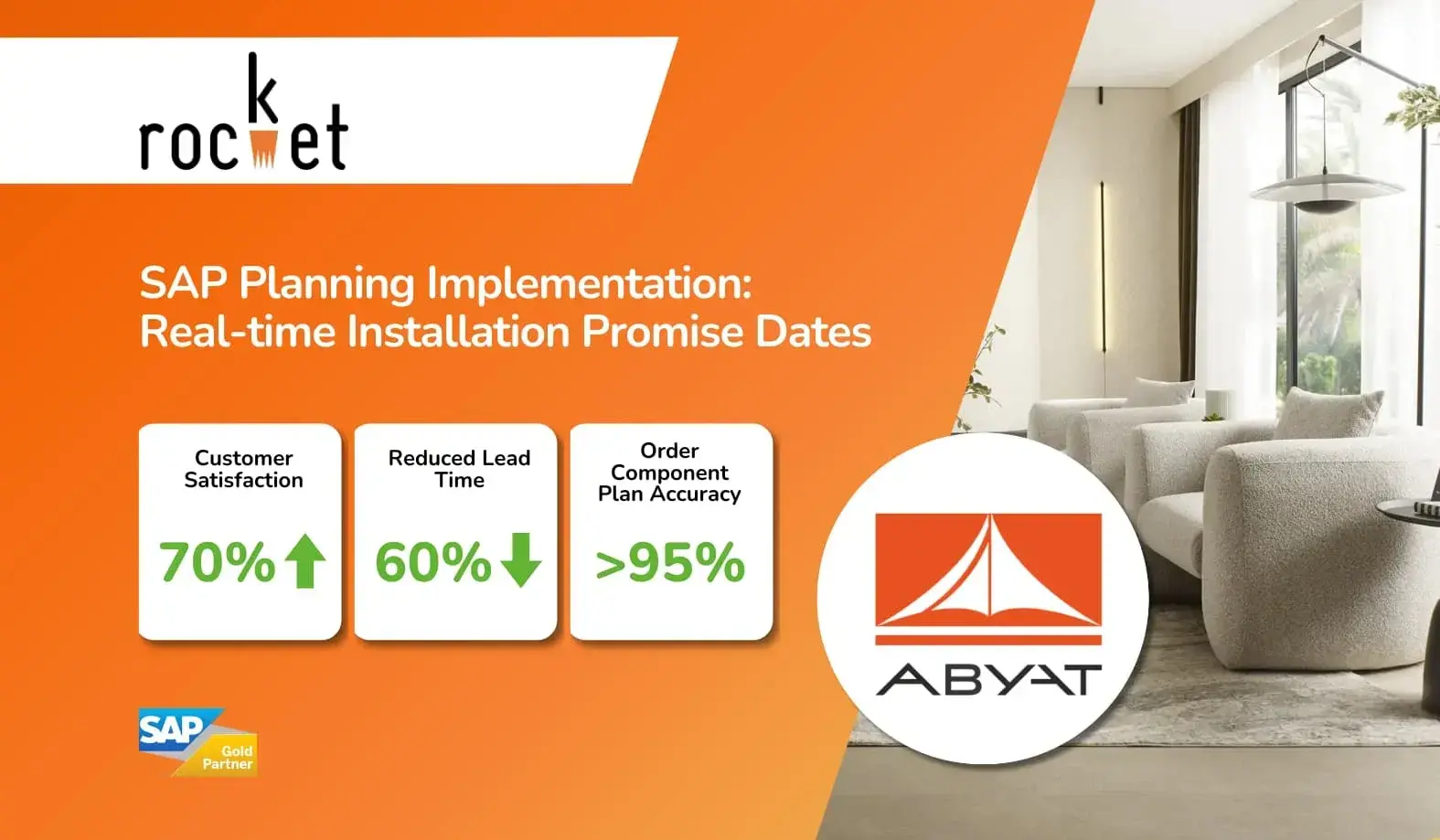
Rocket automates demand-supply processes, cuts lead times from 16 weeks to 2, boosts customer satisfaction by 70%, and achieves real-time planning efficiency for luxury home retailer Abyat.
Abyat is a prestigious chain of luxury department stores operating in Kuwait and Saudi Arabia, known for its high-quality home improvement products, including kitchens, bathrooms, and garden spaces. With a focus on premium offerings and a commitment to exceptional customer service, Abyat has become a trusted name in the luxury home retail market. To meet increasing customer demand and streamline its complex operations, Abyat needed a solution to automate its demand-supply and production planning processes effectively.
Rocket partnered with Abyat to deliver a comprehensive solution across the entire project lifecycle, spanning 18 months. During this time, Rocket’s strategic innovations drastically reduced customer lead times from 16 weeks to just two weeks, leading to a 70% improvement in customer satisfaction. Additionally, Rocket’s implementation enhanced the planning speed, shifting from a 14-day cycle to real-time, immediate responses, enabling Abyat to better align supply with demand and maintain its competitive edge.
The Client’s Challenge: How to Successfully Automate the Demand-Supply and Production Planning Process?
Focus on Delivering Real-Time, Accurate Installation Promise Dates…
Abyat aimed at a solution able to meet a pressing customer need: receiving accurate real-time installation promise dates. The focus of their challenge was to provide reliable dates for installations in real time, effectively impacting not only customer satisfaction but also operational efficiency.
The sales order process needed to include automated checks and complex solutions to correctly calculate promise dates, which could then be communicated in a timely manner, ensuring they were calculated using the most current scheduling data.
… Automating Demand-Supply Synchronisation and Optimising Resource Allocation for Enhanced Production Workflow
In order to guarantee operational efficiency, Abyat required a solution able to impact the demand and supply alignment process, synchronising customer demand with available resources. They needed to implement a process that could automatically check the availability of necessary materials and schedule the required production or installation resources, ensuring the demand could be fulfilled without delays.
Stock transfer processes needed to be automated to timely move inventory between locations (different warehouses, distribution centres, retail stores) based on the material requirements dates and reducing the need for human intervention, so the right products could be available when and where it was requested, speeding up the process.
Automation was key also in the production planning process, the system designed to streamline manufacturing by creating detailed production schedules. It had to take into account both customer requirements and work-centre capacity, ensuring an optimised and efficient production workflow, minimising manual intervention.
Rocket’s Solution: Remote Implementation of Real-time Material Availability for Customer Sales Orders
End-to-End Project Leadership and Optimised APO for Operational Efficiency
Rocket was involved throughout the entire project lifecycle, from initial planning and design to implementation, deployment, and post-go-live support. This end-to-end involvement ensured a seamless transition, reduced risks, and enabled comprehensive alignment of the solution with business objectives.
Rocket evaluated SAP’s Integrated Business Planning (IBP) and Advanced Planning and Optimisation (APO) modules, including Capable-to-Promise (CTP) and Production Planning/Detailed Scheduling (PPDS), using APO-GATP, Global Available-to-Promise. In this instance, maximising the use of standard SAP functionality in APO, Rocket was able to provide a robust, scalable solution that minimised the need for custom development, reducing complexity and future maintenance costs. This implementation enabled the client to instantly calculate and provide accurate delivery and installation dates based on current stock levels, resource availability, and logistical constraints, giving Abyat’s customers a clear and precise timeline for when they could expect their order to be delivered and installed.
By optimising the planning and production processes, Rocket significantly improved operational efficiency, cutting down the lead time for fulfilling customer orders from 16 weeks to just two weeks. This enhancement allowed Abyat to respond more quickly to market demands, reducing inventory costs and increasing customer satisfaction.
Ensuring a seamless go-live experience: Master Data Transformation and User Enablement
Rocket executed a comprehensive overhaul of master data, ensuring it was accurate, standardised, and aligned with the new system requirements. This transformation was critical for enabling consistent and reliable system performance, enhancing data integrity, and supporting improved decision-making across the organisation.
To ensure successful adoption of the new systems, Rocket provided extensive user training. This included tailored training sessions for different user groups, equipping the team with the skills and knowledge necessary to effectively use the new tools and processes, reducing the learning curve and fostering a smooth transition.
Rocket managed the deployment of the solution, ensuring a smooth go-live experience and minimal disruption to ongoing operations. Following deployment, Rocket continued to support Abyat with ongoing optimisation and continuous improvement initiatives, optimising the solution based on user feedback and evolving business needs, thereby maximising long-term value.
Despite the complexities of the project, Rocket executed the entire implementation remotely, with a successful 100% remote delivery model. This approach minimised disruptions, reduced project costs, and demonstrated Rocket’s capability to deliver high-quality solutions without the need for onsite presence, an especially valuable asset during times of travel restrictions and global uncertainties.
Business Success: Key Outcomes of Rocket’s SAP Planning Implementation
The innovative design implemented by Rocket, which maximised the standard SAP functionality in APO-CTP, and APO-PPDS using APO-GATP, yielded significant business outcomes for the chain of luxury department stores, ensuring long-term results by addressing and solving challenges they were experiencing in their SAP-run supply chain.
Business Outcomes:
- Significant Lead Time Reduction: From 16 weeks to just 2 weeks.
- Timely Response for Enhanced Customer Experience: The customer receives reliable and up-to-date installation dates, avoiding delays and inaccurate dates, increasing customer satisfaction by 70%.
- Enhanced Production Planning: From 14 days to immediate; by aligning stock transfers with material requirements dates, it ensures that production runs smoothly without delays.
- Achieving Over 95% accuracy in order component planning.
- Optimised Resource Utilisation: By reserving materials and work-centre capacity automatically, the process prevents resource conflicts and ensures smoother operations.
- Better Inventory Management: The system helps maintain optimal stock levels, reducing the risk of overstocking or stockouts, meaning that materials are available when needed, speeding up the overall supply chain.
Conclusion: Boosting Satisfaction with Accurate Customer Installation Dates
Automated production planning based on customer requirements, work-center capacity and stock transfer processes ensures a well-coordinated manufacturing process that balances customer demand with available resources. This results in better efficiency, reduced lead times, and a more agile production environment.
This alignment process guaranteed by Rocket is crucial for businesses with complex supply chains, as it ensures that demand (customer orders) is always matched with supply (available resources) in a seamless and responsive manner.
Rocket can help companies with a range of SAP planning capabilities, including SAP Integrated Business Planning (SAP IBP) and APO. Get in touch today for a demonstration of how SAP IBP and Advanced Planning and Optimisation (APO) modules can revolutionise your digital supply chain.
Did you enjoy reading our case study? Subscribe for FREE to our Monthly Newsletter to receive SAP Digital Supply Chain insights directly in your inbox!